PARTNER STORY FACING THE FUTURE
相手への思いやりが、自らの技術力向上を生む
切磋琢磨で培った、未来を臨むパートナーストーリー
プラスチック製品の製造・加工並びに販売の事業を展開するキョーラク株式会社様。関東製作所とは、ブロー金型事業で60年以上の長い取引を頂いており、近年、射出金型・成形の方でも特に深いかかわりを持つ企業様です。
この度、キョーラク様のデザイン設計部マネージャー小辻様、生産技術本部マネージャー青木様をお招きし、弊社射出事業本部長の松本と共に、射出成形事業に関しての対談を執り行いました。ブロー金型での取引は長いものの、射出成形事業に関してはまだ5、6年の歴史。しかし今や年間製品立ち上げ20シリーズをも誇る生産力を持ちえたのは、お互いの環境を想いやって取り組んできた結果。
硬い信頼で繋がったパートナーシップが、未来の製造業界をリードします。
AGENDA01
関東製作所はもともとブロー金型専門の会社。
射出成形への参入当時を振り返り、現在との比較は?
弊社射出事業の仕事量増加に呼応するように、関東製作所さんの生産力も上昇。
現在では、関東さんの生産力をバックグランドとして積極的に営業。
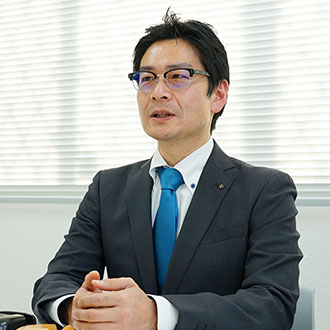
射出事業の参入当時は2011年頃だったと思います。射出金型のみの依頼からスタートし、もともとの「ブロー金型事業からの付き合い」程度の感覚でご一緒させていただいておりました。当時は関東さんには小ロット用の成形機はありましたが、成形が分かる人がいない、設計が出来る人もいない状態だったので、プロジェクト一つこなすのも非常に難儀でしたね(笑)
しかし、松本さんが担当頂くようになった2017年頃からは、かなり一変しました。技術レベルもそうですが、小ロットだけでなく量産をこなすことができるようになってくれたのは非常に大きいと思います。
ちょうどここ数年で弊社の射出事業も大きく仕事量が増えていったのですが、それに呼応するように関東製作所側も専門スタッフの増員、様々な設備・工場の増設により生産力も上がっていった。現在では、関東さんの生産力をバックグランドとして積極的に営業出来ていますね。
加えて、関東製作所さんは無理を聞いてくれる。昔に比べお客様からの検討案提出の期間が非常に短くなり、スピーディーな対応が求められます。さすがにその点は長いおつきあいを経ての信頼関係あってのことですが、お客様側でも製品仕様変更や金型への設変要求は頻繁にあります。
それこそ当時は、「設変データ出しは一週間後になります」という返答もざらでしたが、今では「では次の日に!」というお言葉も多々(笑)。お客様のスピード感についていけるパートナーになっていったと思います。
信頼できるメンバーが樹脂製品業界のプロとして、責任をもって対応します。
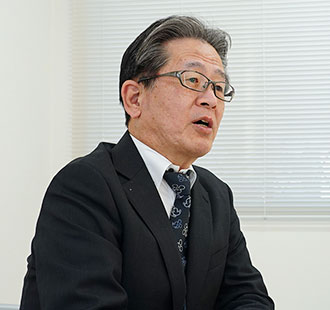
その点は、お客様目線での対応を徹底しています。
時には設変内容と要求納期次第では、社内でパニックになりそうな事案もありますが(笑)、『製品に対する要求形状』と『実現可能な金型設計案』から、最大公約数的な『金型設計案』『製品形状案』を出し、提案することに徹しています。
特にこの5年でそのような体制が取れてきたのは、信頼できるのメンバーを採用し、設計担当や成形担当を固められたことですね。各々が樹脂製品業界のプロとして対応してくれます。
例えば設計担当者と、「このリブ設計箇所、量産時に心配だからこの形状を推したいんだけど?」「これはマズいからこうしようか」など、オンライン会議などを積極的に活用しリアルタイムでCADを動かしながら3D形状を迅速に正確に詰めていきます。
金型目線での最適提案を、3Dデータというカタチで示してくれる。
従来と比べ、お客様への説得力が違いますね。
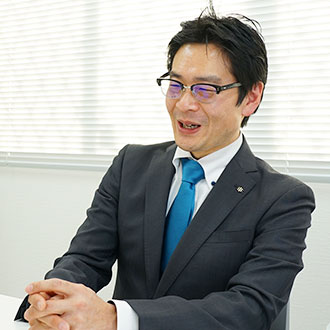
3Dデータに関して言うと、弊社としても3Dデータを積極的に出してくれるのは本当にありがたいですね。他社様ではなかなかそこまで対応してくれるところは少ない。
関東製作所さんは、時には金型目線での実現可能な製品形状を、3Dデータで作って提案として出してくれます。弊社としては、お客様に確認する際にカタチとして見せることが出来るので説得力も出せる。何よりお客様側での「良い悪い」の判断が容易になる。
従来であればお客様から頂いたデータに対して口頭や文面で、どのようにすれば成形品として成立するかをお伝えしておりましたが、それだけでは解釈のズレが生じたりする原因になり、こちらの提案が上手く伝わらない可能性があります。特に近年、プラスチック製品の形状が複雑化している事もあり、難しい案件が増えております。
解析ソフトや技術者の経験・知識を基に検討した、修正を加えた3Dデータを提案してもらえる事で、「何をどうすれば良い」というのがより具体的になり、結果的にやり取りの回数が減り、スピーディーに仕様が固められますからね。
この点は本当に、弊社と関東製作所さんとのタッグならではの強みですね。
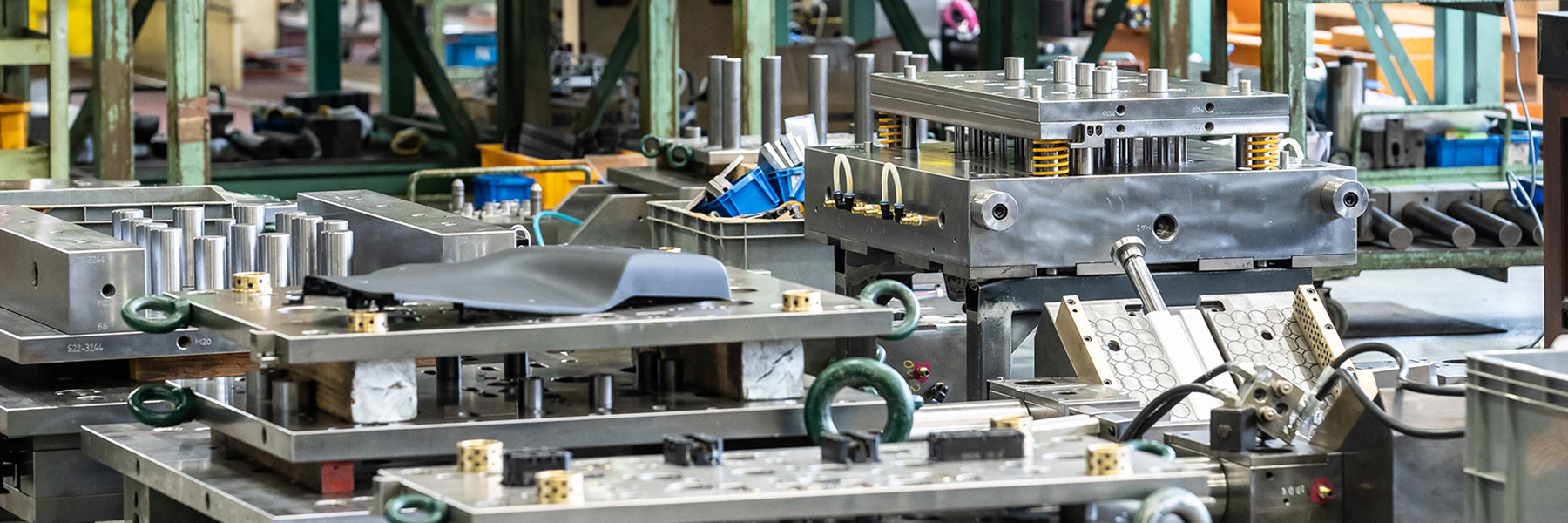
AGENDA02
成形現場と金型現場が同じ工場内にあることが
関東製作所の強み。実際に感じるメリットは?
金型を『成形機からその場で下ろして、横で直してまた載せる。』
3回かかるトライが2回、2回かかるトライが1回で済む。
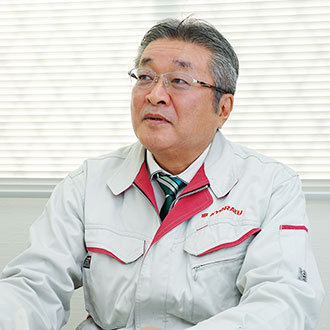
大半の金型・成形メーカーの場合、トライの際にまずは金型メーカーから成形メーカーに金型を送り、成形機に金型を取り付けるところからスタートします。関東製作所さんの場合には、金型と成形現場が併設されているので、トライの立ち合いに行くと既に動作確認済みの金型が取り付けてある状態からスタートできます。
昔だと、現場に行ってそこから段取りして成形機に乗せて…。トライしてみたらエジェクターが一つ動かない!なんてことはざらだったので…。それこそスピードが全然違いますよ。
また、他社の場合のトライでは金型メーカー側のスタッフが工具をもって成形メーカーで控えてくれていますが、当然その場で対応できる金型修正には制限があります。機械に乗せてのメンテナンスが必要な場合には、また金型メーカーに金型を戻して修正をする必要があります。
その点、関東製作所さんのこの環境はその心配が全く無い。金型に不具合があれば、『成形機からその場で下ろして、横で直してまた載せる』がスピーディーに出来てしまいます。
更に最近では、チャック盤(自動取り出し機)がT0の段階で出来ているのも大きい!
通常であればT0でOKが出た後にチャック盤の調整確認が別途かかるので、そこで待つタイムロスが発生してしまいますからね。通常だと、「じゃあここの改修は次回ね」というケースが、その日のうちに出来てしまいます。3回かかるトライが2回、2回かかるトライが1回で済む、そういう状況が作れるので、メリットしかないですね。
金型の取り付けを待たないだけでなく、事前の動作確認、トライ当日には取り出し機まで出来ているので、1度のトライで様々な確認を行い、そこで発生した修正点は、併設の金型加工エリアで即時修正。
一般的なトライの工程 : 金型輸送に伴なう時間的なロスが発生
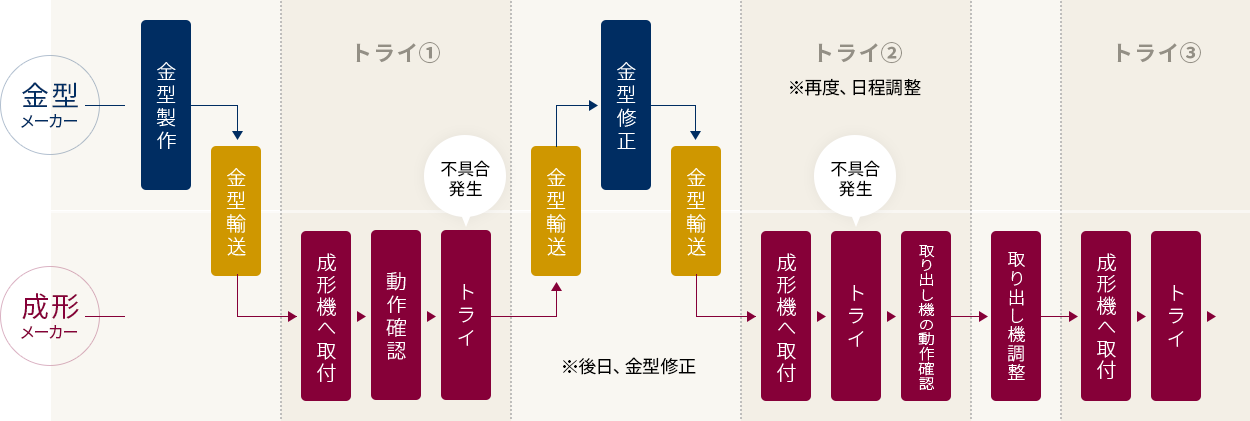
関東製作所でのトライの工程 : 金型輸送が無いことで迅速な対応が可能
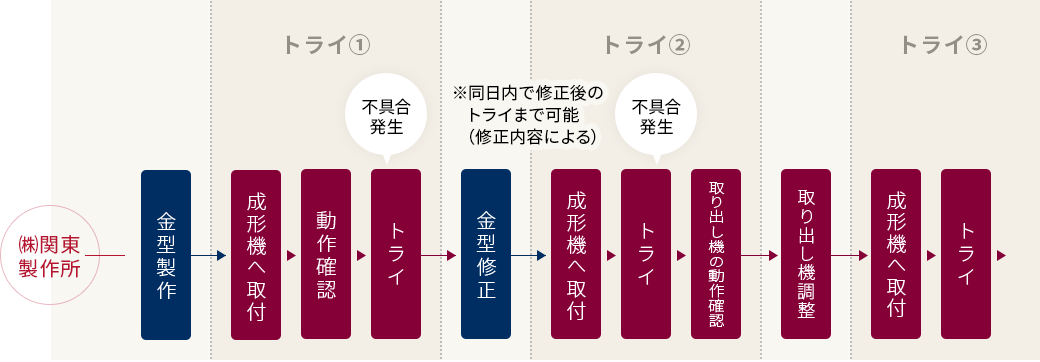
『金型が出来たら、チャック盤も出来ている!』関東製作所の謳い文句です!
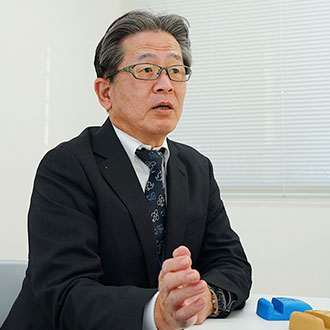
確かにその点は弊社の強みですね。最大限の生産性をこだわっています。近辺で、成形工場、金型工場が丸々くっついている所はかなかな無いと思います。今なら一日で450、850tonの成形機サイズの金型が、最大4型までトライできる程です。成形の担当者が、段取り効率など徹底した仕組みを作ってくれています。
T0段階でのチャック版設置は、2022年からの新しい取り組みです。
実はチャック盤の設計・製作は新入社員に担当してもらっています。CADを一通り覚えた後、流石に曲面設計や金型設計はハードルが高いので、まずは設計力のステップアップとして一連を任せています。チャック盤に関してのパーツ設計から、金型、製品チャック盤の位置関係のシミュレーション。そして自身で発注まで担当させています。
以前はチャック盤による取り出しも個別でトライしていたくらいですからね。それが今では全く不要。我々の狙いとしては、とにかくできるだけ不具合を一度にまとめて出し切ることを目指しています。その点を認めていただけるのは本当に嬉しいですね。
通常の初回トライでは人の手で取出しを行いますが、量産の際には取り出し機で製品取りを行います。人の手の感覚と機械では当然異なる為、「人の手では取り出せた製品が、機械では取り出せない」なんて事もあるので、必ずチャック盤が出来たら確認・調整が必要です。
どうせ確認をするのであれば、初回トライからチャック盤があったほうが、圧倒的に効率的ですよね。キョーラク様の方もこの取り組みを理解して頂いているので、お客様へ事前に取出しの為の保持ピンの確認なども行って頂いているので、更にスムーズになっております。
現状では、全ての製品に対して100%対応できています。「金型が出来たら、チャック盤も出来ている!」のが関東製作所の謳い文句です!(笑)
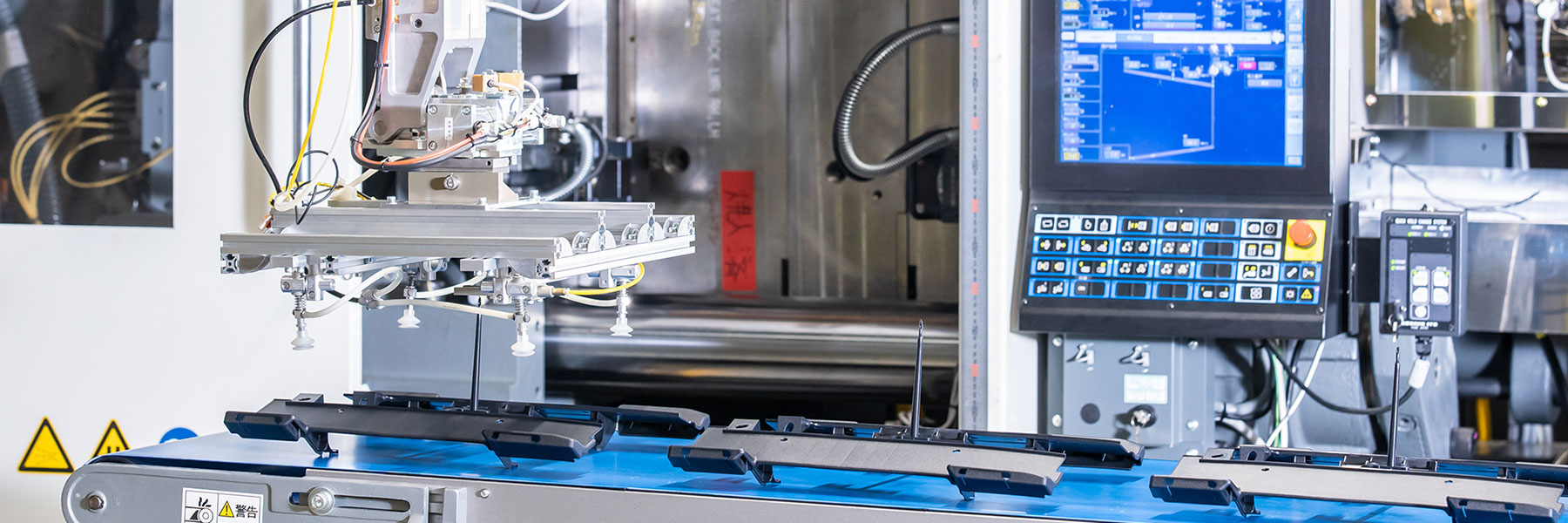
AGENDA03
品質管理にも力を入れる関東製作所の取り組み。
弊社の品質技術への評価は?
この圧倒的な物量の中で納入不良が出てないのは驚きレベル。
必要となれば最適な検査機も自分たちで拵える自己防衛の精神がある。
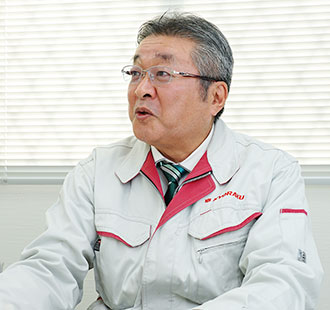
参入したての小ロット中心だった当初と比較すると、現在は品種、生産数も圧倒的に多いのにも関わらず、不良は本当に出ていないですね。私が品質技術を担当したここ数年でも、注意レベルは1~2件出しましたが、納入不良としてのカウントは出していません。この圧倒的な物量の中で納入不良が出てないのは驚きレベルです。
作る技術も上がっているが、品質管理としての見る目が養われていると感じます。検査員の飲み込みも、指導する側もいいのかな。
また関東製作所さんにはメカトロニクス事業部もあるので、必要となれば最適な検査機も自分たちで拵えることができますからね。お客様からの要望はなくとも、ある種の自己防衛として自主的に検査機を造り、ツールをうまく使いながら検査員の指導も徹底されているように感じます。
適材適所の人材配置。そして不良箇所を社内で共通認識化し『検査眼』のレベルアップを。
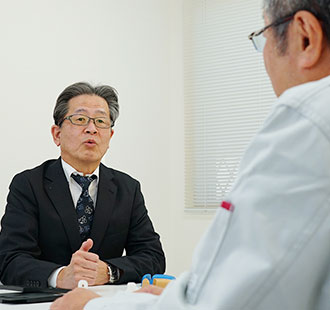
品質管理に関しては、検査する人材のレベルを見極めています。すなわち適材適所の配置です。2次検査の担当にはプロ化出来ているスタッフを配置し、外に不具合が漏らさないことを徹底しています。
また弊社では毎朝行われる「朝会」で、前日に出た工程内不良品を全員で共有しています。日々「これは不良なんだ」というポイントを目で見て認識してもらい、社内の作業者・検査員の検品の目を養い、共通認識化することでレベルアップに努めています。
我々品質技術の立場としても、現場での『作りやすい環境』を提供したい。
そのためにも、お客様とのコミュニケーションを大切に。

我々品質技術の立場としても、現場、つまり作る側での『作りやすい環境』を提供したいと思っています。製品の隅から隅まで100%完璧に抑えるというより、お客様目線で立った「見えない部分はある程度レベルを落とし、抑えるポイントは精度良く抑える」ことの徹底。すなわち『品質管理の適正化』を図りたい。
その為にはお客様とのコミュニケーションを大切にしています。現場側での困りごとや難儀なポイントも、極力お客様にご理解いただく努力も続けていきたいですね。
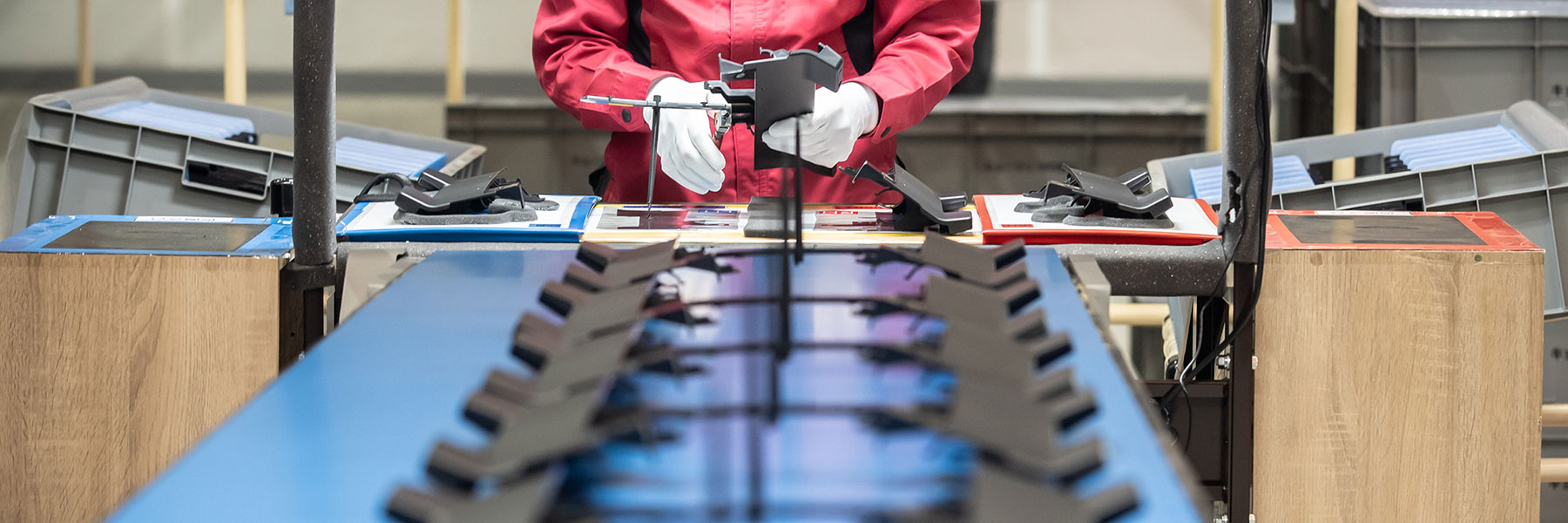
AGENDA04
今、製造業界、特に自動車業界は大きな変革期。
両社において、今後の課題や取り組みたいことは?
更なる短納期開発、そして我々側で製品形状まで作れる力も…。
より一層広い市場での挑戦が求められてくる。
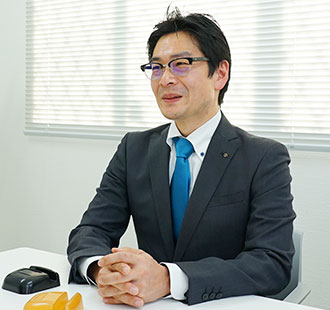
金型事業、成形事業、メカトロニクス事業を持ち、さらにはスタッフの方々にもキョーラクに入っていただき協業させていただいている。安定した作る力がある関東製作所さんだからこそ、我々も積極的な受注活動ができている。本当に頼りにしています。
今後は、更なる短納期開発が要求されてくると思います。また、我々側で製品形状まで作れる力も試されてくるでしょう。近年感じるのは、現状お付き合いいただいているお客様に対しても、樹脂製品以外の分野での開発も担っていいかなければならないということです。金型メーカー、成形メーカーには、より一層広い市場での挑戦が求められてくると感じています。
しかし、弊社と関東製作所さんで進めているこのやり方は間違っていない。まだまだ開拓地を広げられる伸びしろがあると自負しています。
SUMMARY
製品開発のベストパートナーとして“未来”を見据える
今後も関東製作所では「モノづくりの“未来”を創る」為に、お客様により沿った技術開発、体制作りを行ってまいります。
変わりゆく時代の流れに合わせて、お客様の需要を的確にとらえサービスを展開させて頂きます。
お客様の製品開発のベストパートナーとして、関東製作所が選ばれるように日々“未来”を見据えてご対応させて頂きます。