PARTNER STORY FACING THE FUTURE
We have improved our technique with consideration for each other.
Our partnership accumulated by working hard together.
Kyoraku Co., Ltd is the company of manufacturing, processing and selling plastic products. Kyoraku Co., Ltd and KANTO MFG. CORP. have had a long partnership for more than 60 years. We started to work together as blow mold tooling manufacturer, but nowadays we have also worked for injection mold tooling and molding as well.
Matsumoto, Senior Manager of Injection Mold business in KANTO MFG. invited 2 engineers from Kyoraku; Mr. Kotsuji, Manager of Design Dept. and Mr. Aoki, Manager of Production Technology Dept. and talked about injection mold business. Although we have a long relationship regarding blow mold toolings, we have only worked for 6 years in terms of injection mold business. Despite the such a short term, we already have capability of participating in 20 types of automobile. Our strong partnership will lead the future of manufacturing industry.
AGENDA01
KANTO MFG. was originally a blow mold tooling manufacturer.
How do you feel current situation looking back the time of injection mold market entry?
As responding to our business increase, KANTO MFG. increased production capacity.
We now expand our business activities, counting on KANTO MFG. productivity.
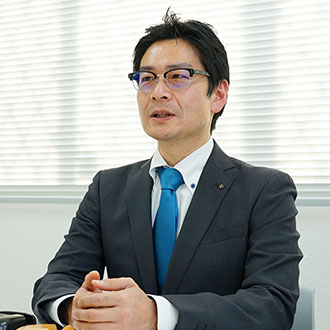
We started injection mold business in 2011. We ordered injection mold toolings to KANTO MFG. for the first time because we already had good relationship on blow mold tooling business. At that time, though KANTO MFG. owned a injection mold machine for small batch, there weren't engineers who know either molding or design. It took so much time to complete a project. (laughs)
But the situation was dramatically changed in 2017 when Mr. Matsumoto started to participate. Technology level of KANTO MFG. greatly got high, and also got capability of mass production.
During the period, we increased the volume of injection mold projects and then as responding to it, KANTO MFG. increased production capacity with more staffs, new equipments and factories. Nowadays, we are counting on KANTO MFG. productivity to expand our business activities.
In addition, KANTO MFG. meets any orders. Since customers recently request our proposal to be shorter than before, we must be polite and speedy. Also customers sometimes change product specifications or designs of mold toolings after design decision. Previously workers at KANTO MFG replied to us "renewed design will be submitted 1 week later." But now they often reply "We'll submit it tomorrow!" (lough) KANTO MFG. is now our partner who can keep up with the customer's speed.
As professionals in the plastic products industry, our reliable members will take responsibility for your business.
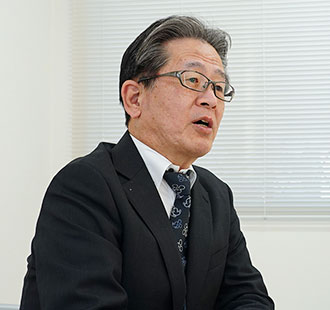
We ensure to work with customer's perspective.
Honestly we are sometime in panic with a tight schedule (lough). But we always focus on the best possible balance between competing factors and then decide "mold tooling design" and "product shapes."
Especially in recent 5 years, we have established current system because we employed trustworthy members to assign dedicated designers and dedicated molding personnel. Each member handles their tasks as a professional of resin production.
Here is our usual conversation; "I am worrying about the ribs design with mass production. How about this one?" "This is not feasible, so we should modify here" or something like that. We smoothly and accurately decide 3D geometry, holding online meetings with sharing CAD in real time.
We appreciate you provide the best proposal with 3D data from perspective of mold tooling manufacturer. It is much more convincing for customers than usual
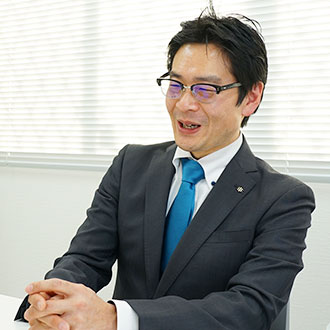
It is very helpful that KANTO MFG. actively submit the 3D datas. There are no other companies to do so.
KANTO MFG. sometimes propose the feasible product shapes from the perspective of mold tooling manufacturer with 3D datas. It is reasonable and easy to make judgement for customers.
We usually explain "how we realize the customer's idea" by word of mouth and writing. But it may cause misunderstanding because the shapes of plastic product recently gets more complicated.
Providing modified 3D data makes it easier to specifically understand "how and what we should modify." Eventually this leads to determine specification speedily.
This is our strength brought from tag team of KANTO MFG. and us.
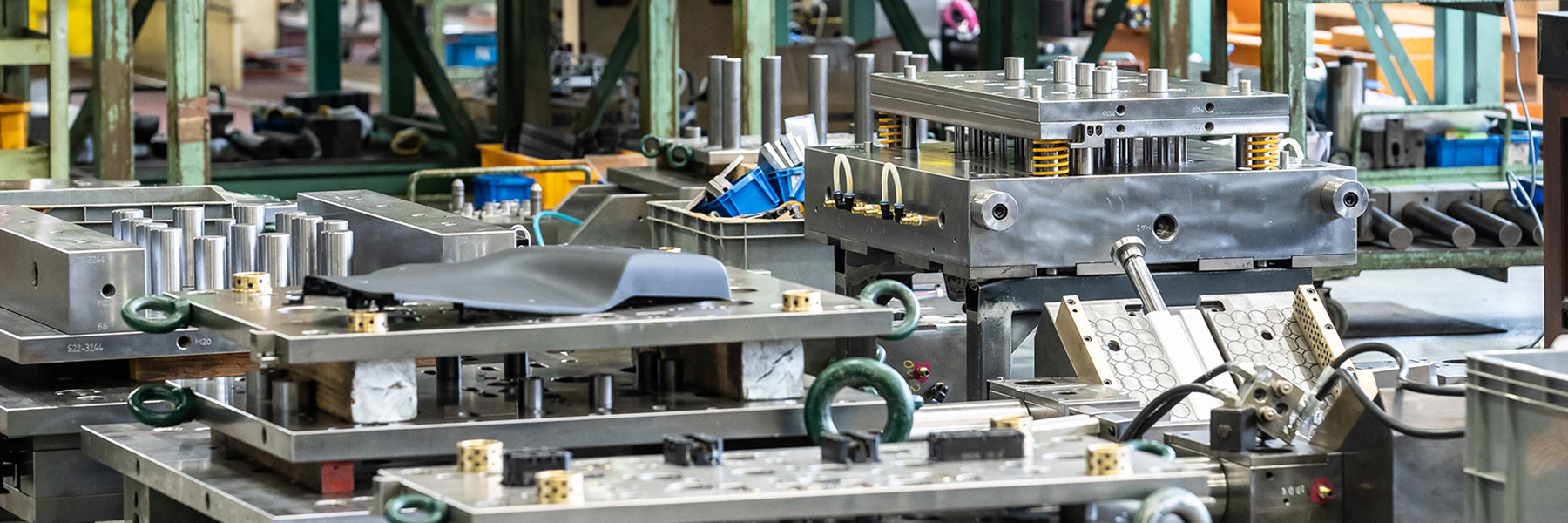
AGENDA02
Our strength is that both molding factory and tooling manufacture factory are in the same site.
How do you technically feel this advantage?
"Remove the tooling from the molding machine and modify it at the same site and re-install it."
Three round trial makes it only two round.
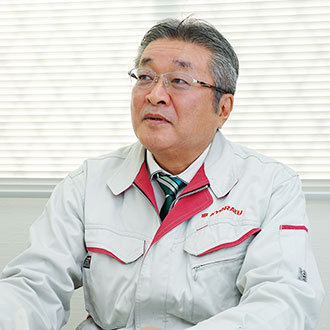
At molding trial, usually a mold tooling manufacturer sends toolings to a molder and attach toolings to mold machines. But in case of KANTO MFG. where tooling manufacture factory and molding factory are in the same site, we don't have to wait for attaching pre-checked toolings to machines and quickly start trial. The speed is much quicker than other company's cases.
When we think about working with other molding companies, the dedicated staffs of a mold tooling manufacturer waits during the trial at molding site. But the modification which can be performed on the spot is not so many cases. In most cases, mold toolings needs to be sent back to a tooling manufacturer and to be modified with machines. It takes long additional time.
In that respect, KANTO MFG. doesn't have that kind of trouble because you have both capabilities molding and tooling manufacture. When the mold tooling should be modified, you can handle the situation speedily like "remove the tooling from the molding machine and modify it at the same site and re-install it to the machine."
Furthermore, it's thankful that KANTO MFG. gets ready for chuck devices (extraction devices) at the time of T0.
Normally, other companies adjust chuck devices after we check that T0 is ok. So, we have to accept our waiting time for preparation chuck devices. They handle most situations like "availability of this modification will be checked next time." But KANTO MFG. can modify toolings at that time. It means that three round trial makes it only two round, two round trial makes it only one round. It is so beneficial.
At the trial, since all settings of tooling attachments, machine's operations and extradict devices are already completed, we can check other various points at the first trial. If the modification points occurred, the mold tooling will immediately be modified at mold tooling manufacture area in the same site.
Trial procedure in other companies : Additional time for tooling transportation occurred.
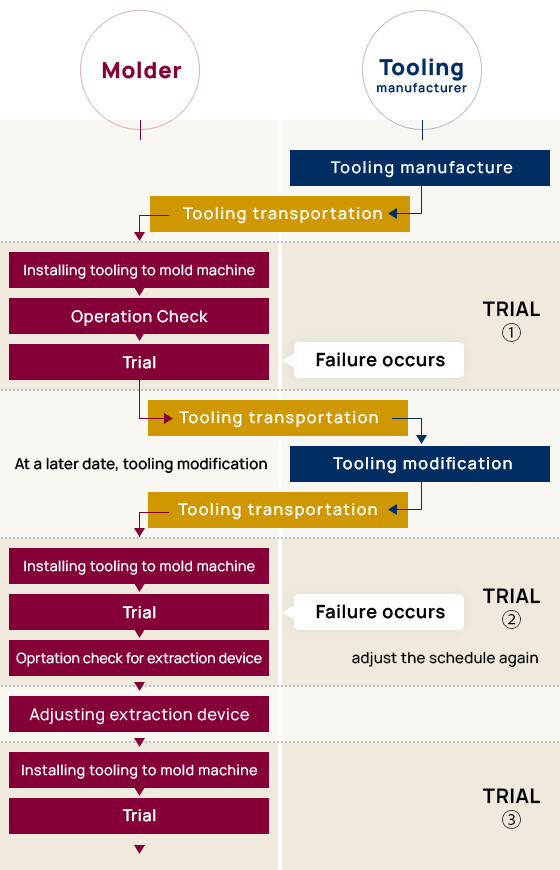
Trial procedure in KANTO MFG. : Quick operation without tooling transporation
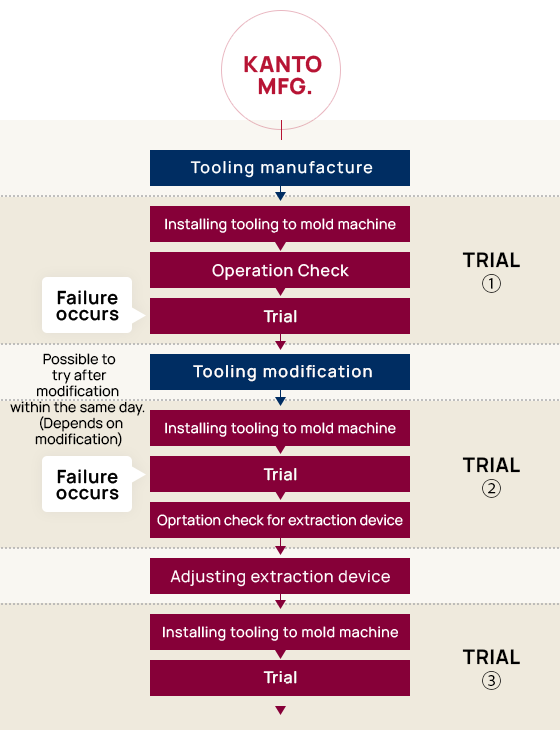
Our motto; " when the tooling is completed, chuck device is also completed."
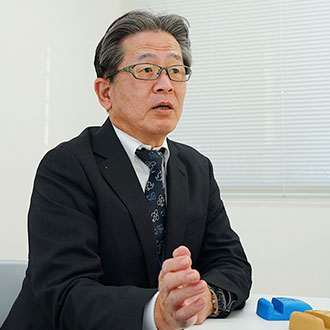
Exactly, we focus on that point as our strength. We pursue the highest productivity. We don't know the other companies where molding factory and tooling manufacture factory at the same site. Nowadays, we can handle trial for up to 4 toolings of 450t/ 850t-level molding machine at the same time. Molding specialists have established the most efficient system.
We have started new effort to get ready for chuck device at the time of T0 since 2022.
We actually assign new employees to design/ manufacture chuck device. After learning CAD operation, they handle all procedure of chuck device from parts design to simulation of positional relationship between toolings and chuck devices, purchase order as a training.
Previously we checked extraction of chuck device itself, but now we don't need the check. We try to bring out all defects at once and are glad that our efforts work well.
We usually extract the product from chuck device at first trial by hand, but in case of mass production, we use extraction machines.Of course there is the difference between hand-operation and machine-operation, so we need to check and modify the chuck device every time.
Since we check chuck device anyway, we prepare for chuck device by first trial so that customers check holding pin to extract products at that time. We believe it is effective way both for customers and us.
We handle this operation for all products so far. This is our motto; " when the tooling is completed, chuck device is also completed."
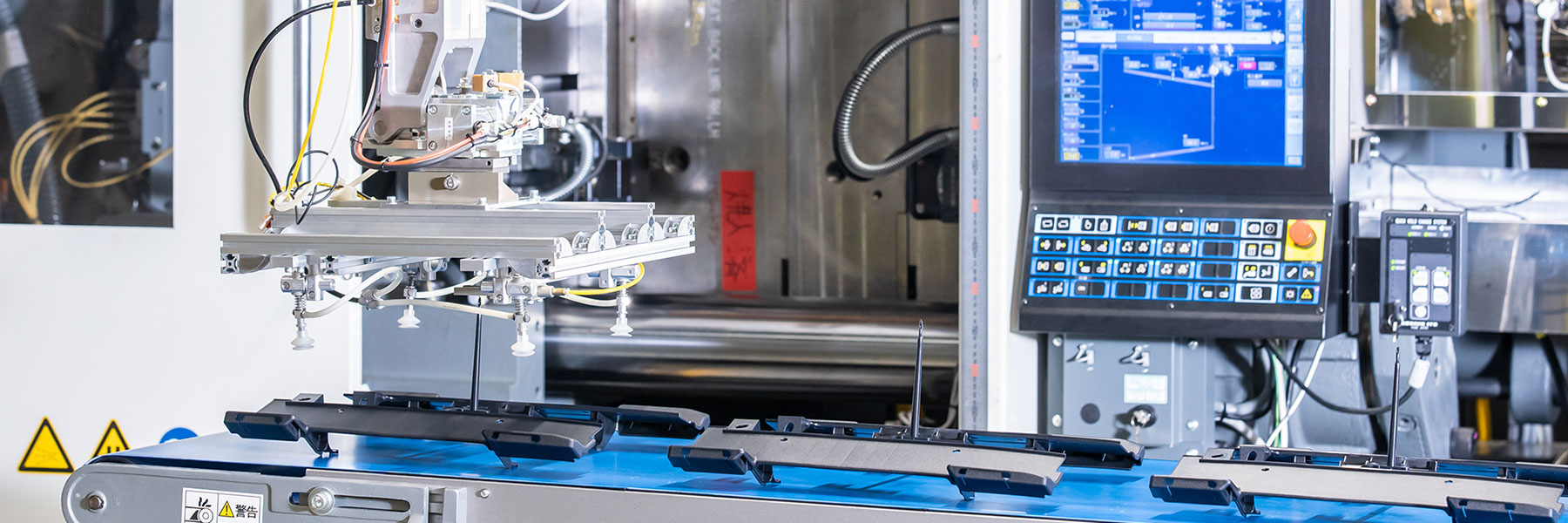
AGENDA03
Our first priority is quality control.
How do you evaluate our quality control system?
It's surprising that no defects are reported through overwhelming amount of products.
You can also manufacture suitable inspecting machines by yourself.
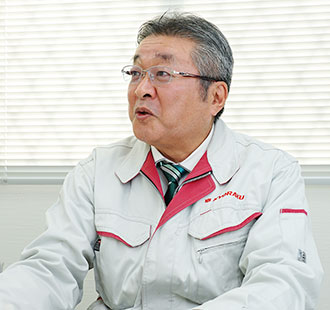
Compared to previous period when entering into injection mold business, KANTO MFG. now handles much more varieties and production numbers. Despite production expansion, defects haven't occured in recent years. Since I became in charge of quality technique a few years ago, I haven't found any defects. It is surprising that no defects are reported through overwhelming amount of products.
I feel that KANTO MFG. has improved not only technology for production but quality control. Probably both inspectors and instructors might be smart.
Also, KANTO MFG. has Mechatronics Dept. to manufacture suitable inspecting machines by yourself. I feel KANTO MFG. independently manufactures inspecting machines as a kind of self defense. Detailed education for inspectors is also your strong point in product control.
Assigning the right people to the right positions.
To develop a clear sense of default and share awareness at the same level.
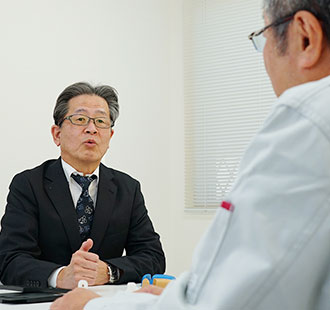
Regarding quality control, we carefully determine inspectors in order to assign the right people to the right positions so they can maximize their potential. We especially assign the seasoned person to secondary inspection not to leak the defaults to outside.
Also we share the previous day's cases of defective production within an operation at every morning meeting. As everyone looks many cases of default daily, workers/ inspectors develop a clear sense of default and share awareness at the same level.
Quality technique Dept. hope the convenient environment for factory workers.
For that, we value communication with customers.

From a perspectives of quality technique Dept., we would like to offer the convenient environment for factory workers. We don't have to completely commit 100% perfectionism, but effectively meet required quality from customers’ perspectives. In other words, we aim "right-level quality control."
For achieving "right-level quality control," we value communication with customers. We try to share our challenges and difficulties from manufacture site with customers.
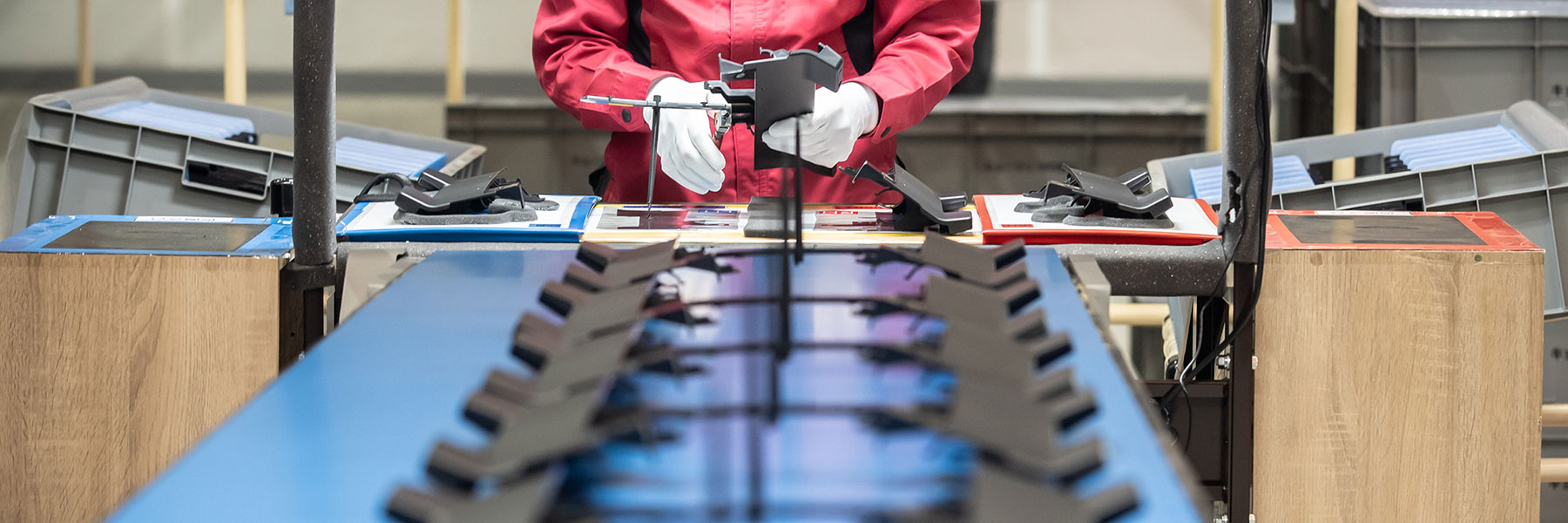
AGENDA04
This is revolutionary period of manufacturing industry especially automobile industry.
What is your challengings and wishes for both companies?
Ability to handle rapid development and to fix product shapes.
We are required to be active in wider market.
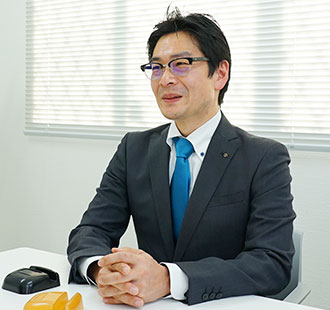
KANTO MFG. has plenty of abilities through Mold tooling manufacture Dept., Molding Dept. and Mechatronics Dept. Also some of your employees temporarily transferred to Kyoraku and work together. We have reliable relationship for a long time. Thanks to KANTO MFG.'s stable manufacturing capacity, we actively enforce marketing activities.
In the future, we are required more rapid developments. Also we might be required the ability to fix product shapes by ourselves. In recent years, we feel our existing customers request us to develop all materials other than resin products. They except molding companies/ mold tooling manufacturers to be active in wider market.
We are sure that our activities work correctly. We will enlarge our market.
SUMMARY
We look confidently the future as a best partner for product development
We will establish the system and technique development for customers in order to create the "Future" of manufacturing.
We will deploy our service to meet customers' demand in accordance with the flow of the times.
KANTO MFG. will support our customers as a best partner for product development, looking ahead to the future.